Make Me PPE: Automated PPE manufacturing management for essential COVID-19 demands
Using Sheetgo, Make Me PPE now save around 780 hours every single year with a custom-made PPE manufacturing workflow to manage national PPE demands and analyze key insights. As a result, they now save over a week per month which they can now focus on producing more PPE.
Finding a way to fulfil and forecast California’s PPE demands
-
Complex, immediate and sensitive information
- Struggle to centralize all data on PPE demand
- Needed a way to forecast demands to analyze trends
From home hobbyists sewing pieces by hand, to high-tech fabrication labs using 3D printing, the Make Me PPE network includes groups producing PPE on vastly different scales. The team was struggling to manually manage all of their PPE requests from multiple sources, then finding a way to divide the requests for each group. The challenge was to provide all parties with an organized, individualized view of PPE demand while maintaining a central database of past and present demand to track and analyze trends. The unique circumstances of the pandemic also created data privacy challenges for the voluntary organization.
“We had incredible difficulty organizing and personalizing views of our data until we found Sheetgo”
Make Me PPE
The team needed an automated system that would allow them to sort PPE demand data from multiple sources by product and team, control who could access sensitive information (such as delivery address and contact details), and provide multiple data views for the different groups of makers. Make Me PPE turned to Sheetgo for this solution, thanks to the great control over private data, as well as the ability to track and record historical data for forecasting.
Automated management for optimized insights and analysis
-
Merge all sources to collaborate on centralized data
-
Append historical data to forecast PPE demands
-
Automations to receive real-time updates across California
Sheetgo built Make Me PPE a unique automated workflow that carries out two main objectives; receive demand updates from various sources so that they can prepare for PPE manufacturing, and analyze and forecast demand by keeping track of previous demand. Firstly, all PPE requests by sources such as the CDC, FDA and the government were delivered using Google Forms. Sheetgo then used the Merge feature to consolidate these requests into a single sheet that the entire team could access. Using Sheetgo filters, the demands were divided for each group, as well as status updates on the progress of each request.
“The separation of data by formatting has increased our productivity and ability to capture data greatly.”
Make Me PPE
Meanwhile, in the same system, Sheetgo’s append setting is used to record and track the historical data of previous PPE demand requests. Make Me PPE could then use this data to analyze and forecast trends for future demands. Finally, the team set up a custom automated schedule that would allow them to receive updates on a very frequent basis, to respond to PPE requests as close to real-time as possible.
Saving 7 days a month to focus on saving lives
-
780 hours saved every year
- 100% control over private and sensitive data
- Centralized data for ultimate accessibility
Thanks to Sheetgo, the Make Me PPE team now have a fully tailored, automated solution that allows them to effortlessly manage manufacturing demands, whilst simultaneously forecasting future demands to get a head start on producing PPE. As a result of this custom project, the team save over 7 days per month on manually inputting and managing data, which they used to focus instead on saving lives through the COVID-19 pandemic.
“Sheetgo has saved us so much time and boosted our productivity. This program has literally helped us save lives!”
Make Me PPE
Make Me PPE no longer have to worry about wasting precious time manually organizing and delegating important PPE demands amongst their groups. Now, they have a completely self-sufficient system that does that for them, whilst maintaining a source of truth with a centralized spreadsheet. What’s more, the team have 100% control over their data to ensure total privacy. Finally, they now have a way to effectively forecast demands so that they are as productive as possible when it comes to protecting people across California.
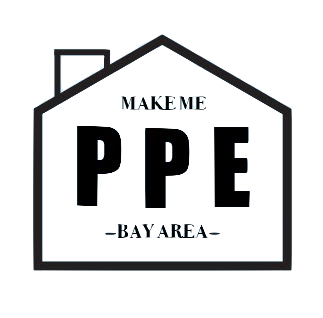
Make Me PPE Bay Area is a grassroots community of sewing enthusiasts in San Francisco producing Personal Protective Equipment (PPE) to help tackle the COVID-19 crisis. The organization’s 500 members have donated over 35,000 units of equipment to more than 150 facilities across California.
USA
Industry
Manufacturing
Manufacturing
Features used
Google Sheets
Google Forms
Google Drive
Merge
Filter
Append setting
Automatic updates
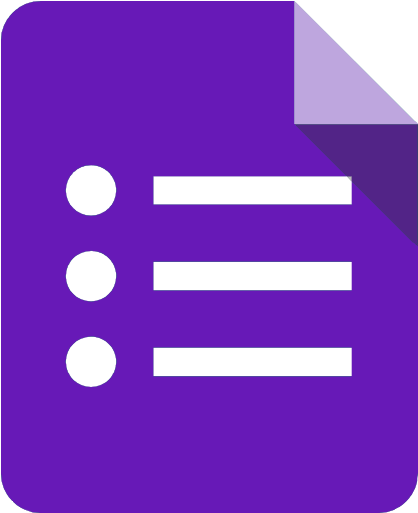
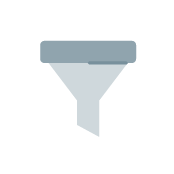
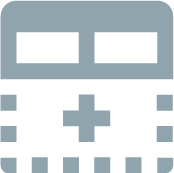
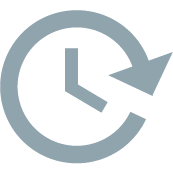